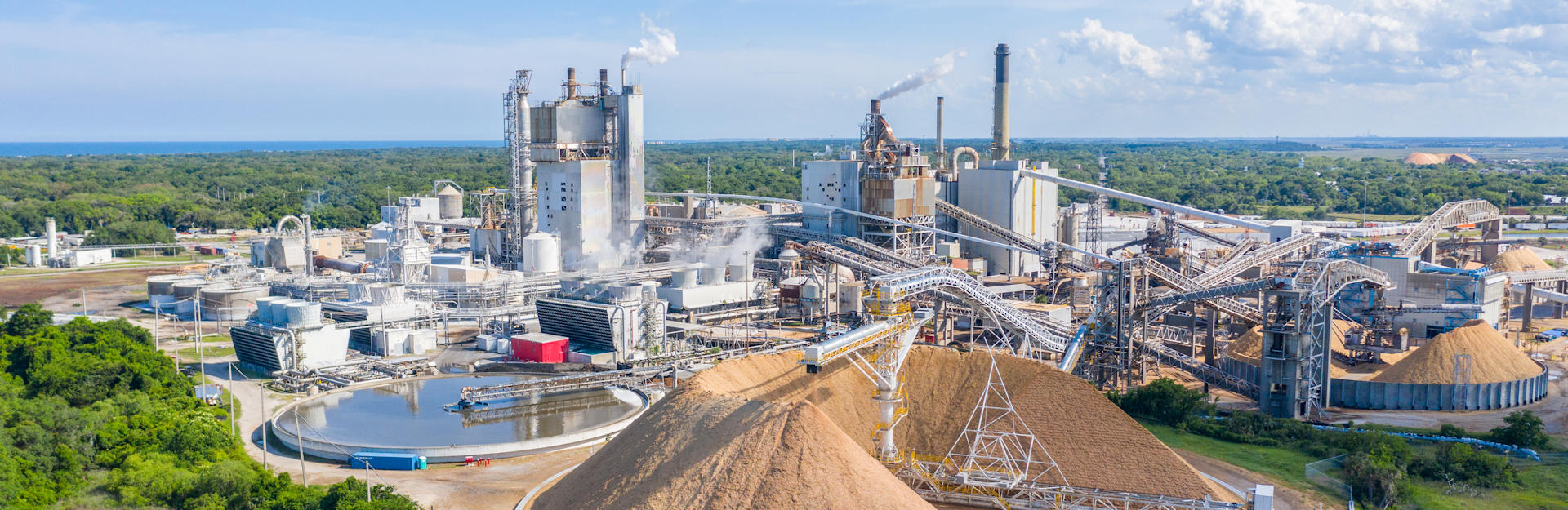
Industries
QSEE are an industrial support tool we work with some of the worlds largest suppliers of raw materials and support them in their journey to reduce their CO2 footprint, improve productivity, waste and costs and in doing so we together make the world a better place.
We work in a series of industries mainly in the manufacture of comodities including within:
By minimizing the standard deviation in cement final product strength, cement residue or with the Kiln operations, a cement plant with an about 1M tonnes per annum capacity can save over $1.5M per annum.
Average savings on a 1.4MT cement plant to be between $M1Y -$M1.5Y in productivity savings, $M0.25Y- $M0.5Y in energy savings and $M0.4Y – $M0.6MY in raw materials per annum.
Explanation – 110KWH is required for 1T, at UK prices of €0.2122/KWH, 5% savings at a 1MT plant means €1,167,100.
We are taking conservative numbers and 2.5% annual savings results in €550,000. Anyway, this is just to show that we are very conservative in the $0.25M-0.5M/Y calculation taking into consideration also electricity price decrease.
Average savings on a 250,000 3m ready mix plant $0.25M/Y- $0.5M/Y in energy savings and $0.4MY- $0.6MY waste reduction per annum.
Damage of pollution (2019) = €38.5/Ton (EU). 0.99 pound CO2 per KWH. Our platform results in a saving ~ €100K per plant for pollution.
Although not an impressive number per se, adding to the energy savings and the reputation/positioning, it has a very positive effect.
CACO3 releases CO2 as part of the cement process hence any reduction in cement usage in a mix will decrease the environmental impact of concrete. QSEE can save a substantial amount per plant.
Waste concrete products can be costly from an environmental perspective to dispose of thus reducing waste by % will show your organisations focus on a greener future.
Productivity and quality in the pulp and paper industry is a key for a profitable mill. While the costs per production hour are rising, you have to prevent unplanned downtime and ensure that all your machines operate at peak performance as well as meet the quality requirements. Not doing so, can cost your mill millions of dollars per year.
This white paper focuses on the successful deployment of Industry 4.0 technology using Artificial Intelligence (A.I) in pulp and paper mill.
**Its prediction rate is 92% and the average time to an event is 40 minutes.**
**The potential business ROI on one production line can reach up to 2M$ a year.**
We are taking conservative numbers and 2.5% annual savings results in €550,000. Anyway, this is just to show that we are very conservative in the $0.25M-0.5M/Y calculation taking into consideration also electricity price decrease.
White paper documents – download here
Enquire for white paper documents
By minimizing the standard deviation in cement final product strength, cement residue or with the Kiln operations, a cement plant with an about 1M tonnes per annum capacity can save over $1.5M per annum.
Average savings on a 1.4MT cement plant to be between $M1Y -$M1.5Y in productivity savings, $M0.25Y- $M0.5Y in energy savings and $M0.4Y – $M0.6MY in raw materials per annum.
Explanation – 110KWH is required for 1T, at UK prices of €0.2122/KWH, 5% savings at a 1MT plant means €1,167,100.
We are taking conservative numbers and 2.5% annual savings results in €550,000. Anyway, this is just to show that we are very conservative in the $0.25M-0.5M/Y calculation taking into consideration also electricity price decrease.
Average savings on a 250,000 3m ready mix plant $0.25M/Y- $0.5M/Y in energy savings and $0.4MY- $0.6MY waste reduction per annum.
Damage of pollution (2019) = €38.5/Ton (EU). 0.99 pound CO2 per KWH. Our platform results in a saving ~ €100K per plant for pollution.
Although not an impressive number per se, adding to the energy savings and the reputation/positioning, it has a very positive effect.
CACO3 releases CO2 as part of the cement process hence any reduction in cement usage in a mix will decrease the environmental impact of concrete. QSEE can save a substantial amount per plant.
Waste concrete products can be costly from an environmental perspective to dispose of thus reducing waste by % will show your organisations focus on a greener future.
Productivity and quality in the pulp and paper industry is a key for a profitable mill. While the costs per production hour are rising, you have to prevent unplanned downtime and ensure that all your machines operate at peak performance as well as meet the quality requirements. Not doing so, can cost your mill millions of dollars per year.
This white paper focuses on the successful deployment of Industry 4.0 technology using Artificial Intelligence (A.I) in pulp and paper mill.
**Its prediction rate is 92% and the average time to an event is 40 minutes.**
**The potential business ROI on one production line can reach up to 2M$ a year.**
We are taking conservative numbers and 2.5% annual savings results in €550,000. Anyway, this is just to show that we are very conservative in the $0.25M-0.5M/Y calculation taking into consideration also electricity price decrease.
White paper documents – download here
Enquire for white paper documents
By applying our technology, you’ll be able to predict the quality of your product’s production at each stage, improve your company’s productivity as well as prevent inventory loss.
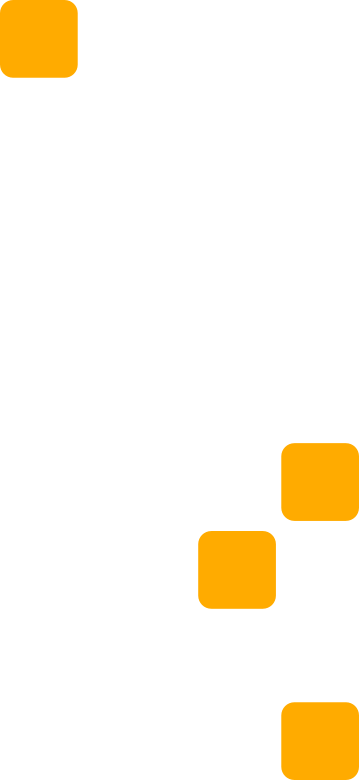
We provide a FREE demonstration to see how our software could have helped your productivity and products quality issues over the past year.
See instantly just how much you could save into the future through our quick and easy trial.
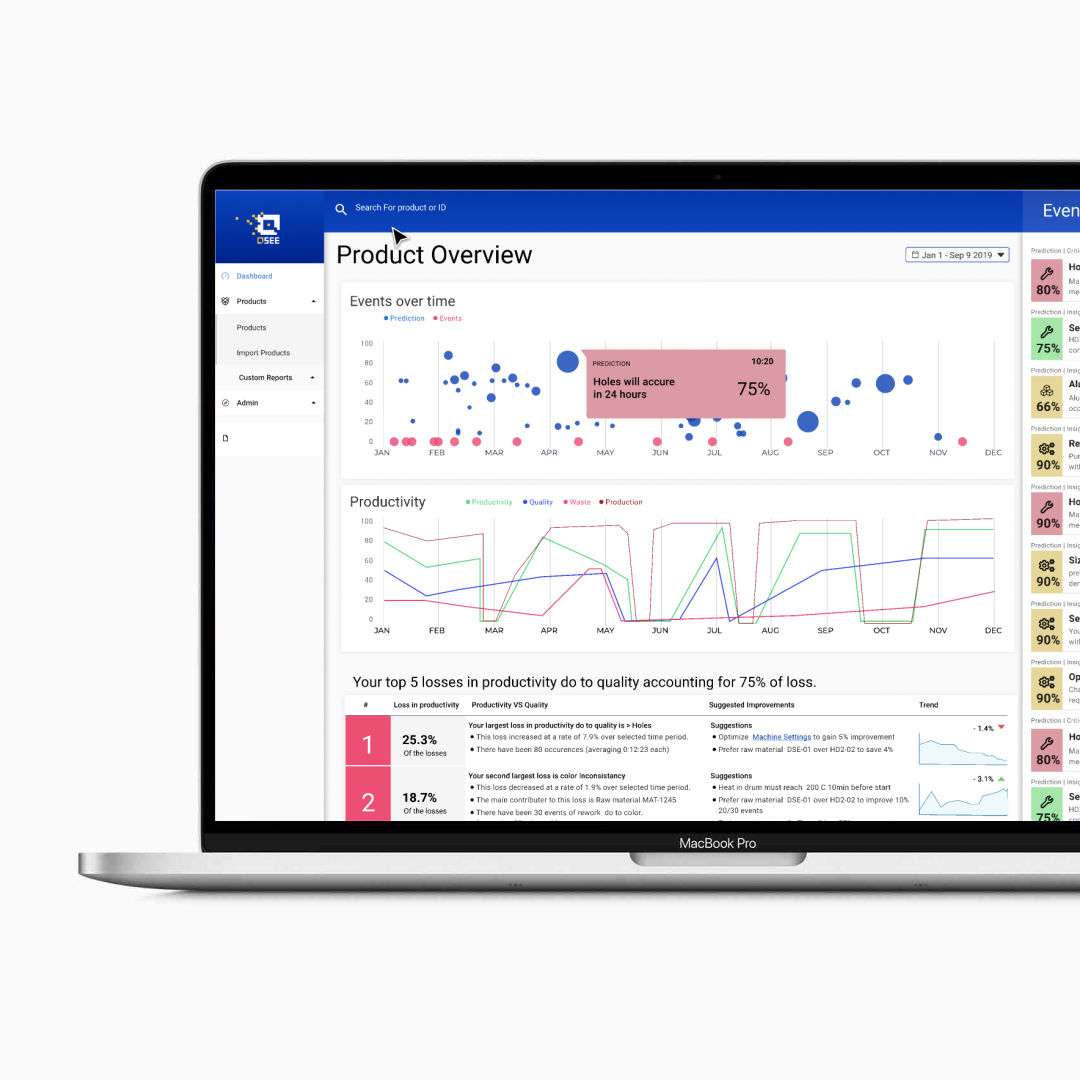